Above and Beyond: The Salute Uniforms' USMC Dress Blue Coat
There’s arguably no military dress uniform in the world that’s as well-known or as much-beloved as the United States Marine Corps “Dress Blues
,” officially designated on page 2-15 in the Marine Corps Uniform Regulations as “Blue Dress ‘B’” for enlisted males (work is underway to introduce a modified version for female Marines). The origin of design elements such as the “blood stripes” on the pants and the Mandarin collar are the stuff of legends, happily passed along to new recruits as sources of pride and inspiration. Another reason for its iconic status is its longevity. While the dress uniforms of other branches of the United States Armed Forces have undergone various revisions over the years—sometimes in a nod to current fashion trends—the Marine’s Dress Blue uniform for enlisted men has remained essentially unchanged for decades. Simply put, it’s a classic.
Still, Dress Blues do share one thing in common with other military uniforms: They must be manufactured to military specifications, or MIL-SPEC for short. MIL-SPEC ensures that all uniforms are identical in appearance and produced with quality materials. Many of the MIL-SPEC standards, such as the types of materials that may be used or the patterns that must be followed for individual uniform components and how they are pieced together, leave no leeway for deviation. But other standards are simply a baseline that was reached in an effort to achieve the dual goals of guaranteeing a quality uniform while keeping costs reasonable.
At The Salute Uniforms, we pored over the MIL-SPEC standards and carefully examined Dress Blues to see what improvements we could make while still adhering to regulations and keeping the price extremely competitive. Many of our enhancements aren’t immediately visible if you simply put a set of our Made-in-USA Dress Blues alongside a set made by a competitor. But when it comes to comfort, durability, functionality, and ease of care, this is definitely a case where beauty is not completely in the eyes of the beholder.
Let’s examine some of the ways in which we’ve gone above and beyond MIL-SPEC guidelines to create the best-fitting, longest-lasting, and most comfortable Dress Blue Coat you can buy.
Collar Me Impressed
One of the hallmarks of this coat is its Mandarin collar, which in addition to contributing to the uniform’s distinct look also hearkens back to the origin of the “Leatherneck” nickname: The uniform regulations promulgated by the Naval Committee of the Second Continental Congress in 1776 specified that Marine uniforms would feature a leather stock, or collar. (Numerous sources state that the collar served the dual purpose of protecting against sword slashes and forcing the wearers to hold their heads erect, but these sources never make it clear if these purposes were spelled out in the regulations or if they're just reasonable inferences.)
The Marine Corps long ago eschewed the use of leather for the collar. Today, the basis of the collar is buckram, a heavy, stiff fabric that’s also used in bookbinding. A strip of felt is attached to the outer edge of the buckram, which is then covered in a fabric that’s also used to form two tabs designed to prevent the metal posts of the two Corps insignia from chafing the wearer’s neck. The fabric is also to create a lip designed to keep the collar’s metallic hook-and-eye fastener from rubbing against the skin.
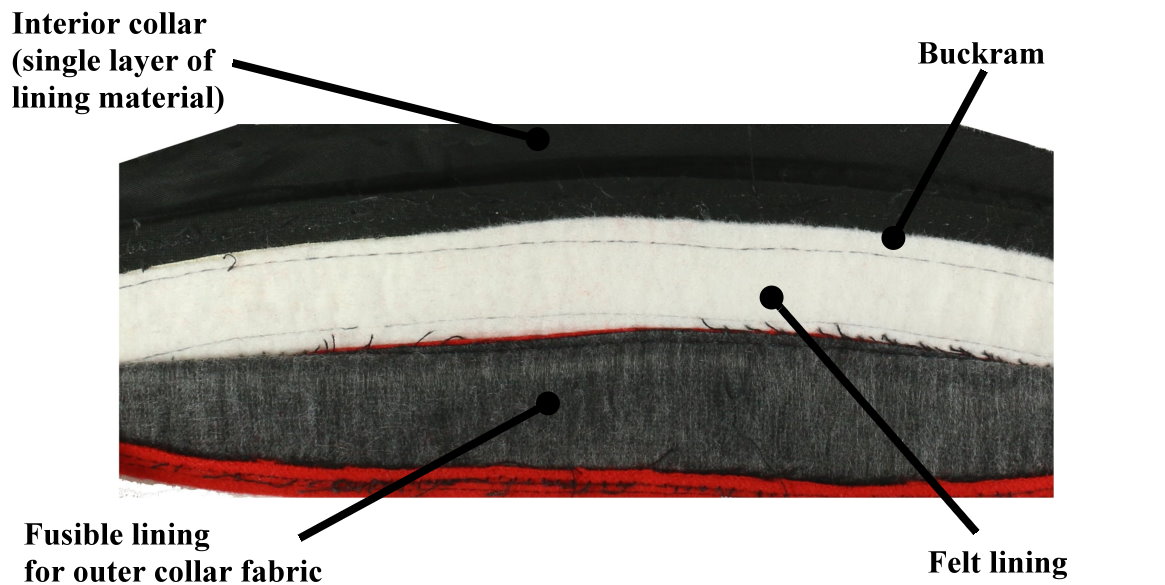 | 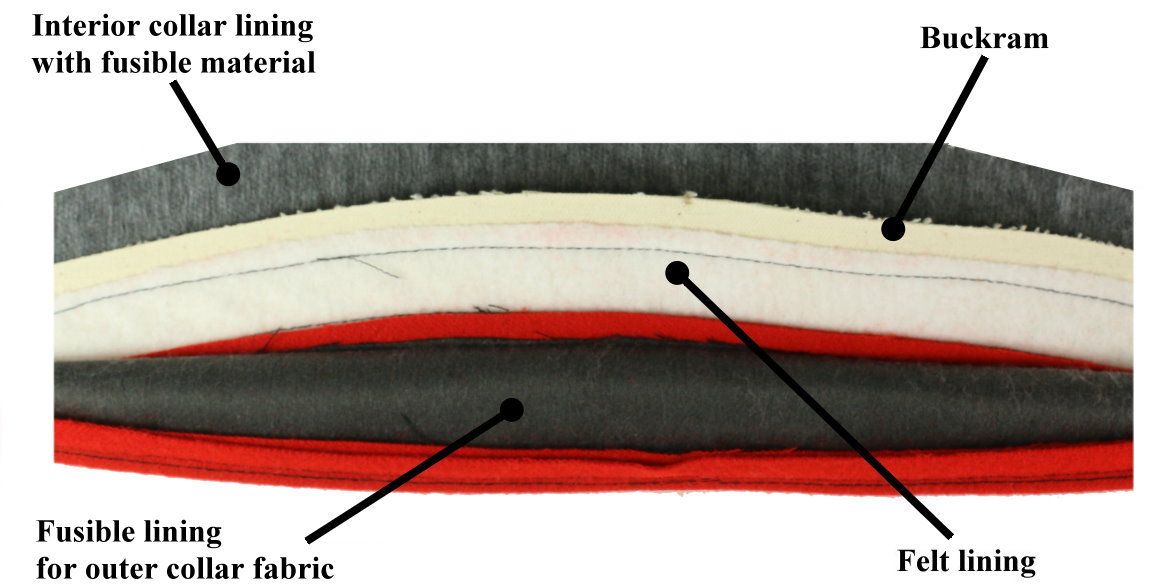 |
Components of USMC Dress Blue Coat Collar — Issue Coat | Components of USMC Dress Blue Coat Collar — The Salute Uniforms Coat |
Unfortunately, the stiffness of the buckram that encourages wearers to keep their head proudly erect can also be uncomfortable. To provide more cushioning between the buckram and the neck, we use fabric fused with a felt-like material to cover the inner as well as the outer edge of the buckram; issue uniforms simply cover the inner edge with very thin fabric. It’s a small enhancement, but its benefits become increasingly obvious with every passing minute a Marine is wearing that tight collar.
Another aspect of the collar that we saw could be vastly improved upon was the construction of those protective tabs for the metal posts of Corps devices and the lip under the fastener. On an issue coat, these components are textbook examples of “bare minimum:” painfully thin pieces of fabric that succeed only in preventing metal from touching skin. Marines are proud to wear the Eagle, Globe and Anchor device on their collars; should they have to suffer to do so?
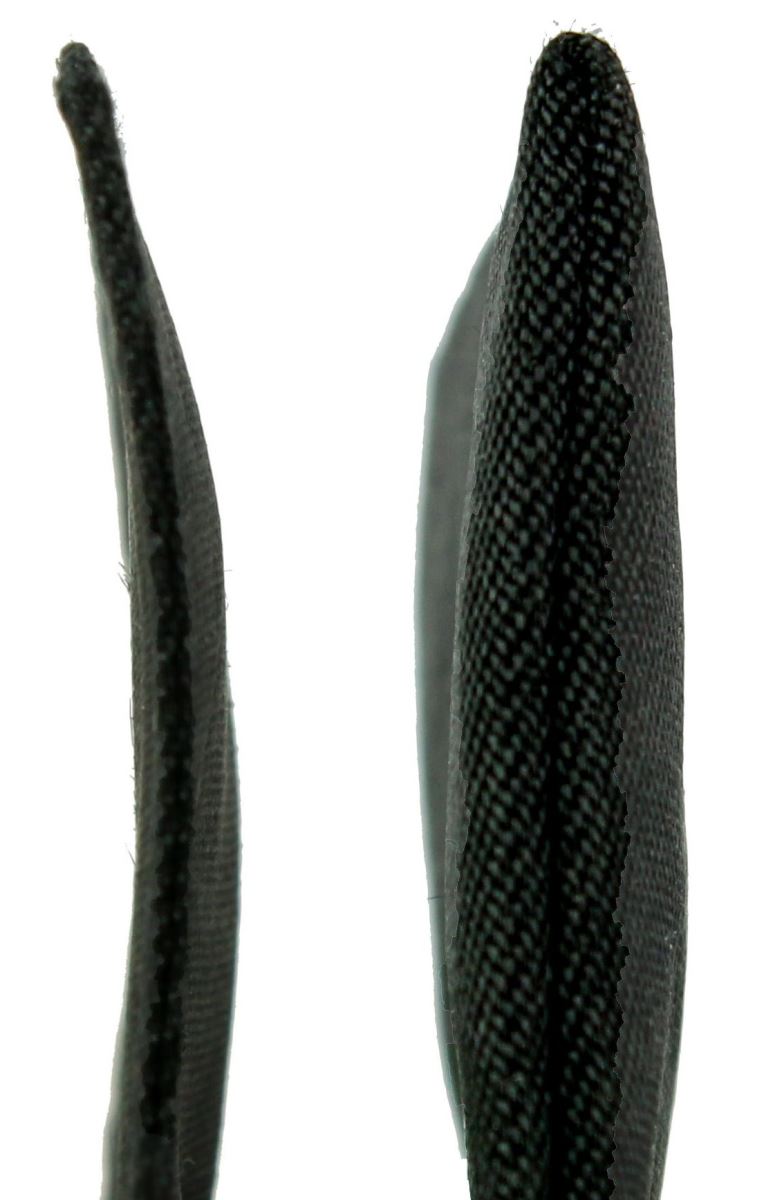 |
Side view of protective tabs for Eagle Globe and Anchor collar devices on the issue coat (left) and The Salute Uniforms coat (right). |
We don’t think so. That’s why the tabs and lip on our Dress Blue collars are generously padded and actually add significantly more comfort in addition to preventing neck abrasions from chafing. Whether you’re mingling at a formal occasion or standing at attention for long stretches at a time, this small improvement yields big dividends.
Full Canvas Coat
Speaking of standing, did you know that your Dress Blue Coat “stands” when you’re wearing it? It’s true—but how well it does so depends on whether the manufacturer merely met the minimum MIL-SPEC Standards, or went beyond them to make sure the coat conforms to your body’s unique shape while still keeping a crisp appearance. To understand why, a short primer on suit-coat construction is in order.
Most folks are aware of the main components of a coat, i.e., the outer fabric and the inner lining. Between these two is an interlining, which usually consists of either a type of material made from horsehair called canvas or a material literally glued to the outer suit fabric called fusible. Also between the lining and outer coat material is a section called the chest piece.
Slightly stiffer than outer fabric, canvas is inserted between the outer fabric and the lining to provide what could be considered a “flexible skeleton”—it helps the coat maintain its basic shape while conforming to your body’s shape without sagging or buckling. The chest piece is a canvas-and-felt reinforced section that covers (you guessed it) the chest area, lengthwise from the arm hole to the middle of your chest and vertically from the collar to just below the pectorals. The area of the coat that comprises the chest piece and extends down to the bottom is called the front panel.
There are three basic types of coat construction: full-canvas, with canvas used in both the chest piece and throughout the entire front panel; half-canvas, where the canvas construction extends just a little below the bottom of the chest piece; and “fused,” where a heat-and-glue process is used to attach another layer of material directly to the outer fabric before the lining is placed over it. Full-canvas coats are understandably more expensive than the other two types, but they last longer and offer a much more natural fit.
We mention this so you can better understand not only what you’re getting when purchase your next Dress Blue Coat, but also why the MIL-SPEC standards are what they are. When you remember that this dress uniform is an issue item—every recruit receives one at boot camp—you can better appreciate the balance that must be struck between ensuring a high-quality uniform and keeping costs within a reason. (In fact, the Corps discontinued issuing the Dress Blue Coat from 1993 to 2007 as a cost-cutting measure.)
.jpg) | .jpg) |
Chest piece exterior, issue Dress Blue Coat | Chest piece interior, issue Dress Blue Coat |
The MIL-SPEC guidelines for the USMC Blue Dress “A” coat call for fused construction, with a chest piece made of a single layer of canvas augmented by an additional crescent-shaped layer of canvas around the armhole (see above). This design provides very little reinforcement for holding multiple medals in place, and consequently many Marines have resorted to using a piece of cardboard as a rigid backstop to prevent the fronts of the uniforms from sagging.
.jpg) |
Front panel with reinforced chest piece, The Salute Uniforms' Dress Blue Coat |
For our Dress Blue Coat, we use full-canvas construction coupled with a chest piece made with two complete layers of canvas—in other words, the second layer covers the entire chest piece, not just the area around the armhole. What’s more, the additional layer is made of even stronger cans, providing extra support to more fully accommodate the weight of several medals. And we don’t stop with a full-canvas construction: we add a wide piece of the non-woven, fusible fabric that we use for pockets over the area of the front panel where the coat buttons are located. This non-stretch material helps the edge of the coat retain its firmness and shape after repeated buttoning and unbuttoning.
While we’re on the subject of buttons….
Buttoned Up
There are quite a few traditions that have sprung up around the Marine Corps’ Dress Blues—but not all of them are happily embraced by the enlisted men who wear the uniform. Case in point: button holing.
The sewn-on brass buttons on the Dress Blues contrast brilliantly with the rich, dark shade of the blouse’s fabric, and they also wonderfully complement the gold-colored chevrons. Unfortunately, they don’t play well with dry-cleaning chemicals, and it’s highly recommended that they be removed before sending them off to the dry cleaner—which means either you or the dry cleaner must sew them on again. And properly resewing these buttons is considerably more time-consuming than replacing a button on your favorite long-sleeve Van Heusen.
Thus was born the ritual of button holing. When it’s time for a set of Dress Blues’ first dry cleaning, Marines often take the coat to a tailor and pay to have the buttons removed and replace them with stitched button holes. It’s a design that makes securely reattaching a button as simple as placing a key on a keyring, and it eliminates the hassle of removing and sewing buttons (or the expense of paying someone to do it). It also makes it a lot easier for Marines to upgrade their coats with anodized, gold-plated buttons.
It’s a wonderful DIY upgrade—so good, in fact, that it made us wonder why the issue Dress Blues doesn’t ship with this feature already in place.
We never did figure out the answer to that question, but rather than spending time investigating to see if lobbyists for the Button Sewers Union were somehow involved, we decided to make this a standard feature on our Dress Blue coats. Whether you’re removing buttons for dry cleaning or simply replacing a lost or damaged button, this design makes the process completely hassle-free—and saves you tailoring expenses to boot.
Sleeves: The Long and Short of It
In Chapter 3 of the Marine Corps Uniform Regulations, we read that “the length of all coats will extend about 1 to 2 inches below the individual's crotch. The sleeve cuff bottom will extend to about 1 inch above the second/large joint of the thumb.”
You don’t have to be a tailor to realize that the odds of an off-the-rack coat simultaneously meeting both those requirements are quite low—which is another way of saying it’s a near certainty that your coat
will need to be altered to conform to regulations. This is true regardless of whether you purchase it from a Marine Exchange, The Salute Uniforms, or another commercial source: The only guaranteed exception is if you have a suit tailored to fit your unique measurements.
Because the regulations regarding the coat’s length are more forgiving than for the sleeve’s length, as well as the fact that arm length varies so widely from person to person, we ship our coats with unfinished sleeves that are usually longer than most customers need. While it costs us extra to add an inch or two of length to each sleeve, we do it for a very simple reason: Sleeves can always be altered to be shorter, but there’s not much you can do if they’re too short to begin with.
Another major issue with ordering a Dress Blue coat with finished sleeves is that when the inevitable alteration takes place, the sleeve ornamentation will have to be removed and sewn back on after the sleeve has been hemmed. Since the red piping on the ornamentation is 100-percent wool and has a tendency to fray—along with the fact that its position on the sleeve means it’s already likely to be exposed to more contact than other parts of the coat—it only makes sense to hold off on sewing on the sleeve ornamentation until the proper length has been ascertained and the sleeve appropriately altered.
So it should come as no surprise that you’ll need to have the sleeves altered. Thankfully, the alteration process will reveal another value-added feature that we incorporate in all the coats we manufacture: the reinforced sleeve.
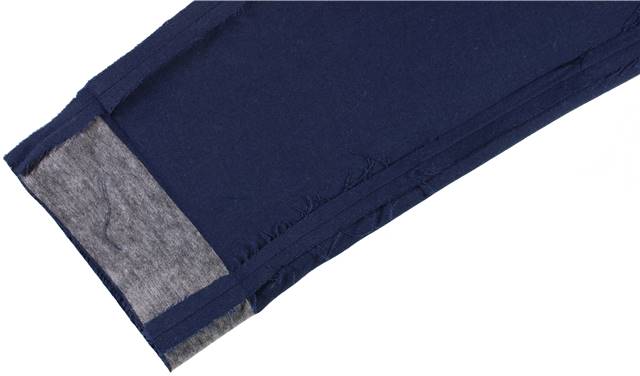 | 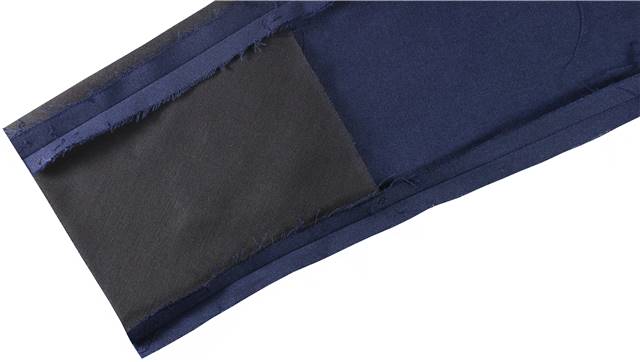 |
Sleeve with strip of fusible material, issue Dress Blue Coat | Sleeve with detachable wigan, The Salute Uniforms Dress Blue Coat |
While all Dress Blue coats are crafted from a fairly durable 55/45 Poly-Wool blend, the ends of the sleeves are nonetheless susceptible to wrinkling or fraying unless they are reinforced with something to augment the natural strength of the outer suit fabric. Manufacturers who simply meet the minimum requirements of MIL-SPEC make a half-hearted attempt to strengthen the sleeve’s end by backing it with a small strip of fusible fabric. Unfortunately, even this minimal reinforcement often winds up on the tailor’s floor as the coat sleeve is shortened—an unavoidable waste because the material is literally fused to the suit fabric and can’t be separated for later reattachment on the altered sleeve.
Our answer to this problem was to reinforce the end of each sleeve with a wide swatch of wigan, a stiff interlining that’s reminiscent of the canvas used in the coat’s chest piece and front panel. When we ship a coat, the wigan is attached only along the two seams of the sleeve. This makes it easy to remove during the sleeve-alteration process, after which it’s fully sewn on to the end of the shortened sleeve. Besides adding much-needed support to this vulnerable area of the coat, this design also ensures that none of the wigan—far more expensive than the paltry strip of fusible used by other manufacturers—winds up on the floor of the tailor’s shop.
Of course, there are circumstances where you might want (or need) to have your Dress Blue coat arrive ready to wear. If that’s the case, we can sew on the ornamentation, service stripes, and chevrons here at our factory, and as part of the process hem the sleeve to conform to regulations. Simply take a coat that fits you as specified in the regulations, measure the sleeve from the seam under the armpit to the sleeve’s end, then give us that information in the “Comments” text box during checkout (you must have selected the chevron/stripes service, of course). Be aware, however, that this means you’ll no longer be able to return the coat for any reason because it has been altered specifically to fit you.
Quality from the Inside Out
A Dress Blue Coat is the epitome of simple elegance. But during the manufacturing process. there’s a whole lot of cutting and sewing going on individual components like the ones we mentioned earlier—collars, sleeves, chest pieces, front panels, and so forth—that are then pieced together.
Open up a standard issue coat, and you’ll see all the seams where these sections are joined. It’s a bit like removing the acoustic tiles from a hanging ceiling in an office or factory; take them away, and all the wires, pipes, and ductwork required to provide electricity, water, and air conditioning are exposed. Over the past couple of decades, it’s become increasingly acceptable to simply forgo the hanging ceiling and leave the guts of the building’s infrastructure exposed. Why? Because it reduces construction costs—which is precisely why the insides of standard issue Dress Blue Coats are only half-lined.
Now, a case could be made that exposed infrastructure in a building’s interior is also a stylistic choice (“office Steampunk,” perhaps), but the same can’t be said for the half-lining: There’s absolutely nothing appealing about seeing where and how many sections are sewn together to create this classic coat.
That’s why we go beyond MIL-SPEC and use a full lining not just for the Dress Blue coat, but also for every dress uniform coat we manufacture. A fully lined interior maintains the sharp, professional, and dignified appearance of this classic uniform, befitting of the honor and commitment displayed by the Marine who will be wearing it for years after the initial purchase. We also go a step further and employ fusible material behind the lining for those parts of the coat that aren’t supported by canvas. In contrast, some MIL-SPEC coats—already bereft of canvas save for the chest piece—have no interlining at all for the bottom third of the coat (the “skirt”).
The Bottom Line
We’re proud of the discreet refinements we’ve made to the Dress Blue coat and will continue to search for even more ways we can make it as comfortable and durable as possible. For now, though, we leave you with one simple fact: No matter where you shop or what you pay, you won’t find a more finely crafted Dress Blue coat than the one we manufacture at our plant outside Greensboro, North Carolina.
Period.